Commercial Appliance Repair
Introduction
Commercial Appliance Repair
A. Hey, today we are going to understand how to take care of our appliance, check the details, you can start by emphasizing the significance of appliances in our daily lives. we will discuss how they make our lives more convenient efficient and easy
B. let’s focus on the frustration and inconvenience caused by appliance breakdowns, emphasizing the importance of timely repair and maintenance.
C. On the basis of Do It Yourself few common sense of techniques need to discuss
D. “Utilizing my extensive experience in the repair and service industry, I can confidently state that a critical insight for a successful appliance repair business is recognizing a fundamental truth: among a pool of 100 devices, approximately 70% of issues or faults arise due to mishandling, negligence, and human error. Essentially, every piece of equipment, machinery, and appliance undergoes meticulous design and manufacturing, integrating an array of precautions before entering the market. Through rigorous testing across varying conditions, they prove to be exceptionally reliable and rarely experience immediate failures.
actually, Friends, The occurrence of spontaneous failures under normal circumstances is exceedingly improbable. Instead, concerns typically revolve around ordinary wear and tear, consumable items, battery lifespan, fluctuations in electrical input, and replaceable components. In essence, it’s comparable to subjecting these products to a comprehensive crash test.
Starting an Appliance Repair Blog Business:
Comprehensive Guideline
I. Introduction to Launching a Mobile and Commercial Appliance Repair Business
A. Recognizing the Relevance of Appliance Repair Services
B. Exploring the Market Demand and Opportunities
II. Market Research and Strategic Planning
A. Conducting In-Depth Market Analysis: Identifying Target Customers and Competitors
B. Crafting a Solid Business Plan: Defining Services, Pricing Models, and Unique Value Proposition
C. Establishing Clear Business Objectives and Milestones
III. Legal and Administrative Essentials
A. Business Registration and Legal Structure: shop act,MSME Registration Necessary Licenses and Permits
B. Comprehensive Business Insurance for Protection
C. Implementing Efficient Bookkeeping and Financial Management Systems
IV. Skill Enhancement and Professional Development
A. Evaluating Current Skill Set and Identifying Skill Gaps
B. Pursuing Relevant Training, Certifications, and Workshops
C. Mastering a Wide Range of Appliance Repairs and Troubleshooting Techniques
V. Tools, Equipment, and Inventory
A. Compiling a Comprehensive List of Essential Repair Tools
B. Establishing Reliable Sources for Quality Spare Parts and Consumables
C. Investing in Safety Gear and Personal Protective Equipment
VI. Setting Up a Functional Workshop or Service centre
A. Selecting an Ideal Location: Accessibility and Adequate Space
B. Designing an Efficient Repair Workshop/Service Center: Organized Layout and Equipment Placement
C. Ensuring Adherence to Safety Standards and Regulations
VII. Crafting a Strong Brand Presence
A. Developing an Engaging Business Name and Distinctive Logo
B. Establishing a Robust Online Footprint: Website, Social Media, and Online Listings
C. Launching Effective Marketing Campaigns: Local Advertising, Promotions, and Referral Programs
VIII. Delivering Outstanding Customer Service
A. Prioritizing Exceptional Customer Experience: Prompt Communication and Transparency
B. Implementing Stringent Quality Control Measures: Thorough Testing and Inspections
C. Offering Warranties and offering pick and drop services also Post-Service Support to Build Trust
IX. Pricing Strategy and Revenue Generation
A. Formulating Competitive Pricing Models: Flat Rates, minimum service charges, labour charges, Hourly Charges, and service and Consultation Fees
B. Exploring Additional Revenue Streams: Maintenance Contracts, special service camp, Upgrades, and Value-Added Services, Referal Service Coupon
C. Monitoring Financial Performance and Flexibly Adjusting Strategies
X. Scaling and Expanding the Business
A. Regularly Assessing Business Performance and Gathering Customer Feedback
B. Scaling Operations by Hiring Trained Staff and Delegating Tasks
C. Exploring Opportunities for Growth: Geographic Expansion, New Services, and Partnerships
XI. Conclusion: Embracing the Appliance Repair Entrepreneurial Journey
A. Reflecting on Milestones Achieved and Lessons Learned
B. Emphasizing the Need for Ongoing Learning, Adaptation, and Innovation
Explanation:
This comprehensive guide outlines the steps to initiate and grow an appliance repair business:
Market Research and Planning:
Understand the market and competition, creating a solid business plan with services and value proposition.
Legal and Administrative:
Register the business, secure insurance, and establish financial systems.
Skill Development:
Assess skills, undergo training, and gain expertise in various appliance repairs.
Tools and Equipment:
Gather necessary tools and reliable parts sources, prioritizing safety gear.
Workspace Setup:
Choose a suitable location, design an organized workspace adhering to safety standards.
Branding and Marketing:
Create a strong brand through name, logo, online presence, and effective marketing.
Customer Service:
Provide exceptional service, quality control, warranties, and post-service support.
Pricing and Revenue:
Set competitive prices, explore additional revenue streams, and monitor finances.
Scaling and Expansion:
Evaluate performance, hire staff, and explore growth opportunities.
Conclusion:
Reflect on accomplishments, embrace ongoing learning, and emphasise adaptation and innovation for sustained success.
Mobile And Appliances Repair Blog:
A. Mobile appliance repair: Identify common problems that mobile device users often face, such as battery drain, frozen screens, or connectivity issues.sim card, network issues, and
B. Provide step-by-step troubleshooting tips for each issue, including restarting the device, checking for software updates, clearing the cache, and resetting network settings.
C. Mention specific troubleshooting techniques for popular mobile operating systems (e.g., Android, iOS).
Commercial Appliance Repair: Mobile
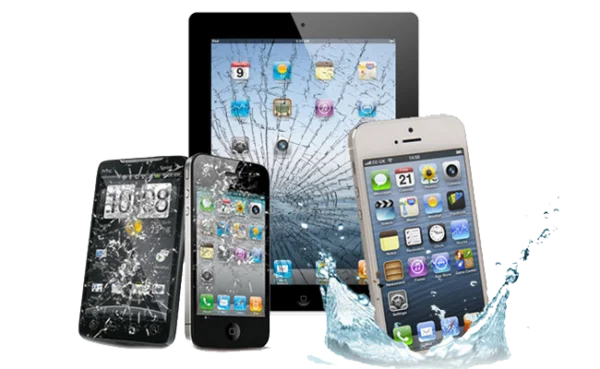
Mobile Appliance Repair :
Fault Finding and Troubleshooting
I. Introduction to Mobile Appliance Repair
A. The Significance of Mobile Devices
B. Fundamentals of Mobile Components
II. Tools and Equipment
A. Essential Tools for Mobile Repair
B. Safety Protocols and Guidelines
III. Common Mobile Issues
A. Power-related Problems
B. Challenges with Charging
C. Troubles with Display
D. Audio and Speaker Complications
E. Connectivity Glitches
IV. Faults Finding and Troubleshooting
A. Initial Assessment
1. Physical Damage Inspection
2. Gathering User Information
B. Testing and Diagnostic Tools
1. Uses of Digital Multimeter
2. Uses of Opening Tools, Hot Air Soldering Gun, Solder iron
3. Software, Testing Cables and Connectors and BGA IC chip/IC
C. Identifying Fault and Daigonoces the Problem
1. No Power/Dead: Pinpointing Battery, PCB track, circuit level component Problem or Charging and BGA IC Issues
2. Charging Problems: Locating Faults in the Charging Port, Battery, or Charging IC
3. Display problems: Identifying Problems with LCD, Connector, Touchscreen, or Display IC
4. Audio and Speaker Problems: Tracking Down Speaker, Microphone, or Audio IC Issues
5. Network Problems: Spotting Wi-Fi, Bluetooth, or Network IC Issues
6. Software Issue: Software need to upgrade/flashing required
D. Step-by-Step Troubleshooting
1. Carefully to check and do fault finding, identify the Issue
2. Thoroughly Testing Components and Connections
3. Replacing Faulty Components
E. Reassembly and Thorough Testing
1. Ensuring Precise Reassembly
2. Rigorous Functional Testing
V. Tips for Successful Repairs
A. Handling Fragile Components B. Effective Management of Screws and Parts C. Appropriate Application of Heat during Repairs
VI. Advanced Troubleshooting
A. Diagnosing Software-Related Problems
1. System Resets and Updates
2. Identifying Malware or Virus-Induced Issues
B. Evaluation of Water Damage 1. Drying and Cleaning Strategies
VII. Repair Skill Development and Practice
A. Learning from market Real-technician
B. Enhancing Confidence through Dedicated Repair Practice
C. Staying Abreast with the Latest Mobile Models
VIII. Conclusion
A. Significance of Proficiency in Mobile Repair
B. Encouragement to Explore and Expand Knowledge
This outline provides a clear structure for creating a comprehensive mobile repair guide centered around fault finding and thorough troubleshooting explanations. You can expand on each section with detailed insights, practical suggestions, and visual aids to craft a valuable resource for those interested in learning about mobile repair.
LED and LCD TV Commercial Appliances Repair
A. Discuss common issues faced by LED and LCD televisions, such as no picture, distorted display, or sound problems.
B. Provide troubleshooting steps, such as checking connections, adjusting picture settings, or resetting the TV.
C. Advise readers on when it’s appropriate to seek professional help, especially for complex technical problems or hardware failures.
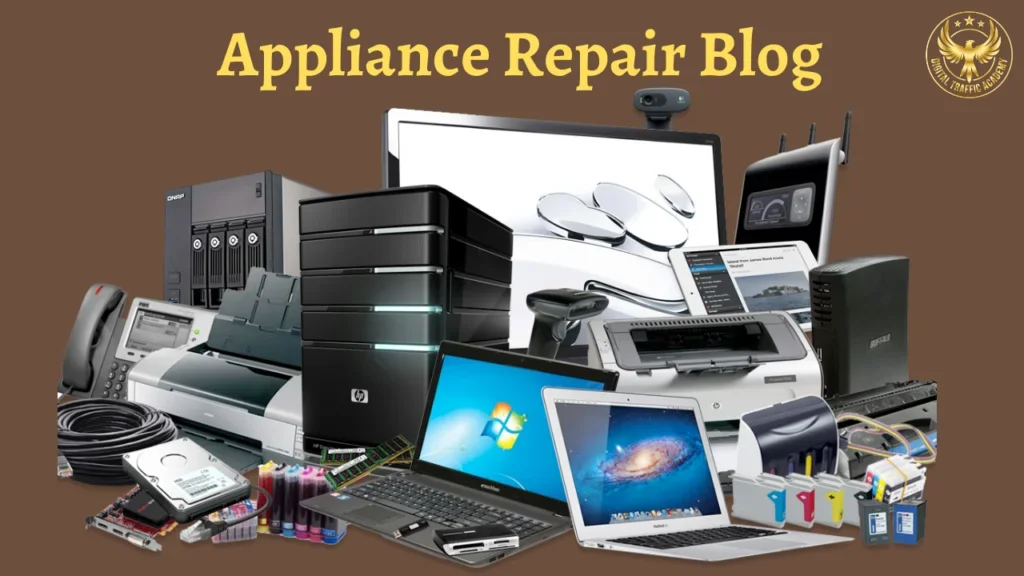
LED and LCD TV Appliances Repair Guideline : Fault Finding and Troubleshooting
I. Introduction to LED and LCD Television Repair
A. Significance of LED and LCD Televisions B. Basic Components of LED and LCD TVs
II. Tools and Equipment for Television Repair
A. Essential Repair Tools for LED and LCD TVs B. Ensuring Safety During Repairs
III. Common Problem in LED and LCD Televisions
A. Power-Related Problems
B. Display Anomalies (Blurry, Flickering, No Image)
C. Audio Troubles (No Sound, Distorted Audio)
D. Connectivity Concerns (HDMI, Wi-Fi, Ports)
E. Backlight Challenges (Dim, No Backlight)
F. Troubles with Remote Control
IV. Fault Finding and Troubleshooting Process
A. Initial Evaluation
1. Checking External Factors (Power Source, Cables)
2. Gathering User Input B. Utilizing Diagnostic Tools
1. Multimeter for Voltage and Resistance Checks
2. Schematic Diagrams and Service Manuals
C. Identifying the Specific Issue
1. Power Problems: Investigating Power Supply or Mainboard
2. Display Anomalies: Assessing LCD Panel, T-Con Board, or Mainboard
3. Audio Issues: Examining Audio Circuit, Speakers, or Mainboard
4. Connectivity Concerns: Analyzing Ports, Cables, or Mainboard
5. Backlight Issues: Scrutinizing LED Strips or Inverter Board
6. Remote Control Troubles: Inspecting IR Receiver or Mainboard
D. Step-by-Step Troubleshooting Approach
1. Isolating the Problematic Component
2. Testing and Replacing Faulty Parts
E. Reassembly and Final Testing
1. Ensuring Proper Reassembly Techniques
2. Conducting Thorough Functional Tests
V. Tips for Effective Television Repairs
A. Handling Fragile Components Safely B. Documenting Disassembly Progress C. Decoding Schematic Diagrams and Service Manuals
VI. Advanced Troubleshooting Strategies
A. Addressing Software Issues and Firmware Updates
1. Resetting TV to Factory Settings
2. Updating Software for Enhanced Performance B. Diagnosing Network and Smart TV Functionality 1. Tackling Wi-Fi Connection Challenges
VII. Practice and Skill Enhancement
A. Learning from Real-Life Repair Scenarios B. Boosting Confidence Through Practical Experience C. Staying Abreast of Evolving TV Technology
VIII. Conclusion
A. Significance of Proficiency in Television Repair B. Encouragement to Continuously Explore and Learn
This outline provides a clear structure for creating a comprehensive guide on LED and LCD television repair, focusing on fault finding and thorough troubleshooting explanations. You can expand each section with detailed insights, practical tips, and visual aids to craft a valuable resource for those interested in learning about television repair.
Refrigerator Commercial Appliances Repair :
Fault Finding and Troubleshooting
I. Introduction to Refrigerator Repair
A. The Importance of Functional Refrigerators B. Understanding Key Components in Refrigerators
II. Tools and Equipment for Refrigerator Repair
A. Essential Repair Tools for Effective Repairs B. Prioritizing Safety Measures During Repairs
III. Common Refrigerator Issues
A. Addressing Cooling Problems B. Tackling Frost or Ice Accumulation C. Investigating Unusual Noises and Vibrations D. Dealing with Water Leaks and Puddles E. Managing Temperature Inconsistencies
IV. Fault Finding and Troubleshooting Process
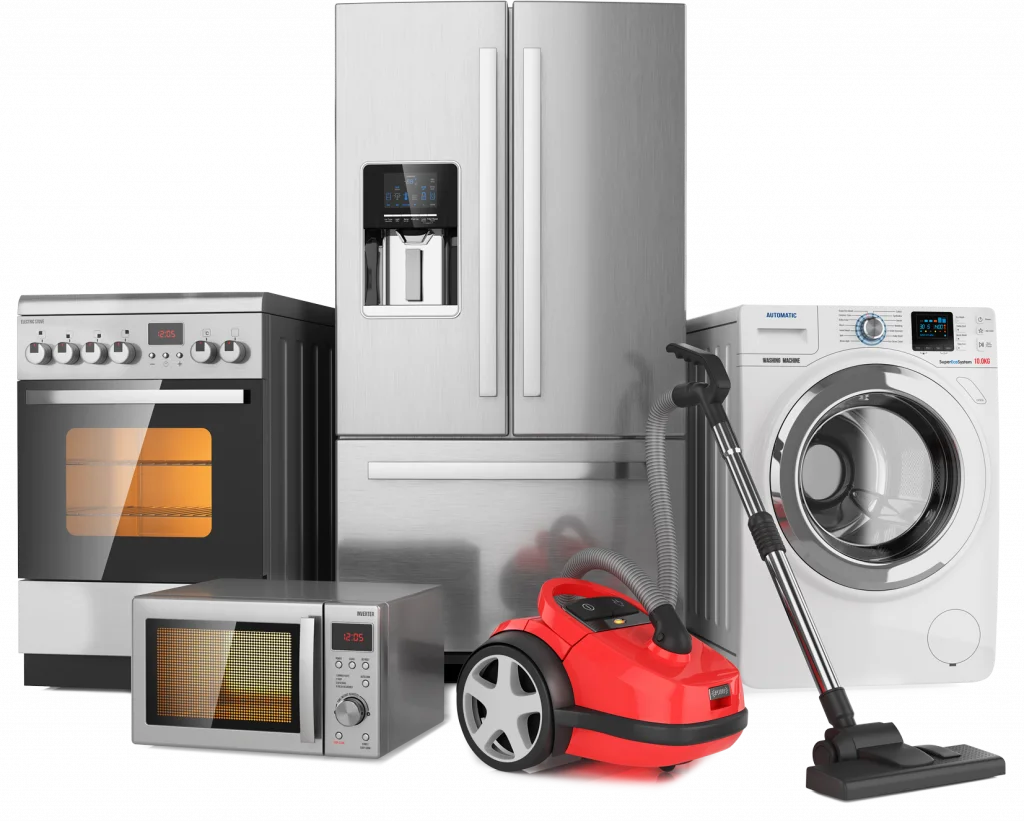
A. Initial Evaluation
1. Ensuring Power Availability and Connections
2. Gathering Relevant Problem Details from Users
B. Diagnostic Tools Utilization 1. Leveraging Multimeters for Electrical Checks 2. Using Thermometers to Measure Temperature
C. Identifying the Specific Issue
1. Cooling Issues: Analyzing Compressor, Evaporator Fan, or Thermostat
2. Frost Buildup: Investigating Defrost Heater, Defrost Timer, or Defrost Thermostat
3. Noise and Vibrations: Examining Condenser Fan, Evaporator Fan, or Compressor
4. Water Leakage: Assessing Drain Pan, Drain Tube, or Water Inlet Valve
5. Temperature Fluctuations: Understanding Temperature and Damper Controls
D. Step-by-Step Troubleshooting
1. Isolating the Precise Problem Area
2. Thoroughly Testing and Replacing Faulty Components
E. Reassembly and Final Testing
1. Adopting Correct Reassembly Techniques
2. Carrying Out Comprehensive Functionality and Cooling Tests
V. Tips for Effective Refrigerator Repairs
A. Ensuring Safety When Handling Refrigerants
B. Documenting Disassembly Steps and Wiring Connections
C. Grasping the Fundamentals of Refrigeration Systems
VI. Advanced Troubleshooting Strategies
A. Addressing Control Board and Electronics Problems
1. In-depth testing of Control Boards and Circuits
B. Diagnosing Refrigerant and Sealed System Issues
1. Detection and Resolution of Refrigerant Leaks and Blockages
VII. Practice and Skill Enhancement
A. Learning from Real-Life Repair Scenarios B. Building Confidence Through Practical Experience C. Staying Updated with Refrigerator Technological Advancements
VIII. Conclusion
A. Recognizing the Significance of Refrigerator Repair Proficiency B. Encouragement to Keep Learning and Exploring Continuously
Feel free to expand on each section with your insights, tips, and explanations to create a comprehensive refrigerator repair guide
Air Conditioning Commercial Appliances Repair :
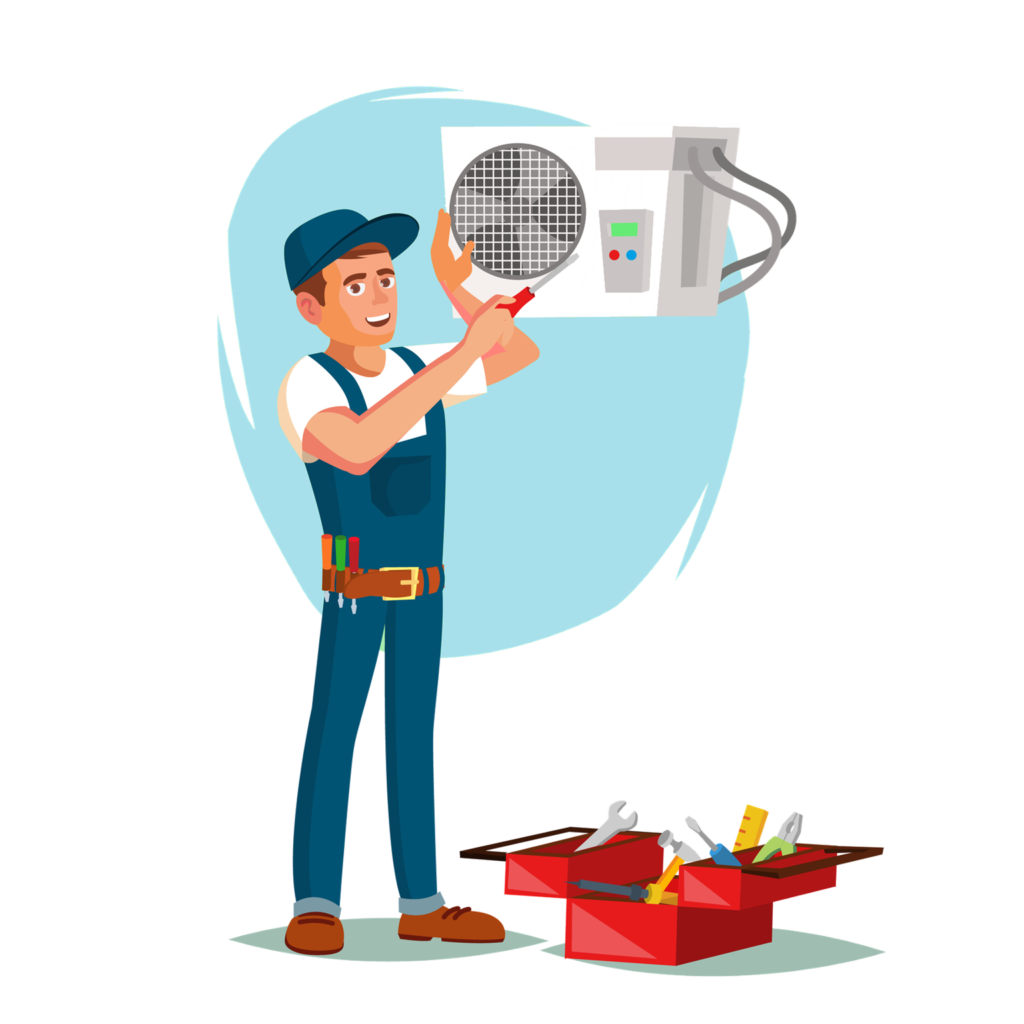
Air Conditioning Commercial Appliances Repair :
I. Introduction to Air Conditioning Unit Repair
A. Significance of Maintaining Functional Air Conditioning Units B. Overview of Essential Components in Air Conditioners
II. Tools and Equipment for Air Conditioning Unit Repair
A. Key Tools Necessary for Effective AC Repairs B. Prioritizing Safety Measures Throughout the Repair Process
III. Common Air Conditioning Unit Issues
A. Addressing Cooling Deficiencies or Complete Lack of Cooling B. Dealing with Insufficient Airflow or Weak Air Circulation C. Investigating Unusual Noises and Annoying Vibrations D. Managing Leakage of Water or Unwanted Moisture E. Resolving Electrical Malfunctions and Power-related Challenges
IV. Fault Finding and Troubleshooting Process
A. Initial Assessment of the Problem 1. Verifying Adequate Power Supply and Electrical Connections 2. Gathering Precise and Detailed Problem Descriptions from Users
B. Utilizing Appropriate Diagnostic Tools 1. Using Thermometers to Gauge Temperature Readings 2. Employing Multimeters to Inspect Electrical Components
C. Pinpointing the Root Cause of the Issue 1. Tackling Cooling Problems: Analyzing Compressor, Condenser, Refrigerant Levels 2. Handling Airflow Troubles: Inspecting Air Filters, Blower Fan, Ductwork 3. Addressing Noises and Vibrations: Examining Fan Blades, Motor, Bearings 4. Solving Water Leakage: Scrutinizing Drain Pans, Drain Lines, Condensate Pump 5. Resolving Electrical Glitches: Evaluating Capacitors, Relays, Wiring
D. Systematic Troubleshooting Steps 1. Isolating the Specific Culprit Affecting Performance 2. Rigorous Testing and Replacement of Defective Components E. Ensuring Proper Reassembly and Final Testing 1. Skillful Reassembly Techniques and Thorough Cleanup 2. Comprehensive Testing of Cooling Performance and Airflow Functions
V. Tips for Effective Air Conditioning Unit Repairs
A. Ensuring Safety While Handling Refrigerants
B. Detailed Documentation of Disassembly Procedures and Wiring Connections
C. Grasping the Basics of AC System Operation and Refrigeration Cycle
VI. Advanced Troubleshooting Strategies
A. Addressing Advanced Issues like Control Board and Sensor Problems 1. Exhaustive Examination of Electronic Components and Circuitry
B. Expertly Diagnosing Refrigerant Leaks and System Efficiency 1. Methodical Identification and Resolution of Refrigerant Leaks and Blockages
VII. Repair and Skill Development with Practical Experience
A. Gleaning Insights from Real-Life Repair Scenarios and Case Studies
B. Building Confidence and Competence Through Hands-On Practice
C. Staying Abreast of the Evolving Trends in Air Conditioning Technology
VIII. Conclusion
A. Recognizing the Value of Proficiency in Air Conditioning Unit Repair
B. Encouragement to Embrace Continuous Learning and Exploration
Feel free to develop each section with your knowledge, advice, and explanations to craft a comprehensive and informative air conditioning unit repair blog/guide.
Washing Machine Commercial Appliance Repair :
Fault Finding and Troubleshooting
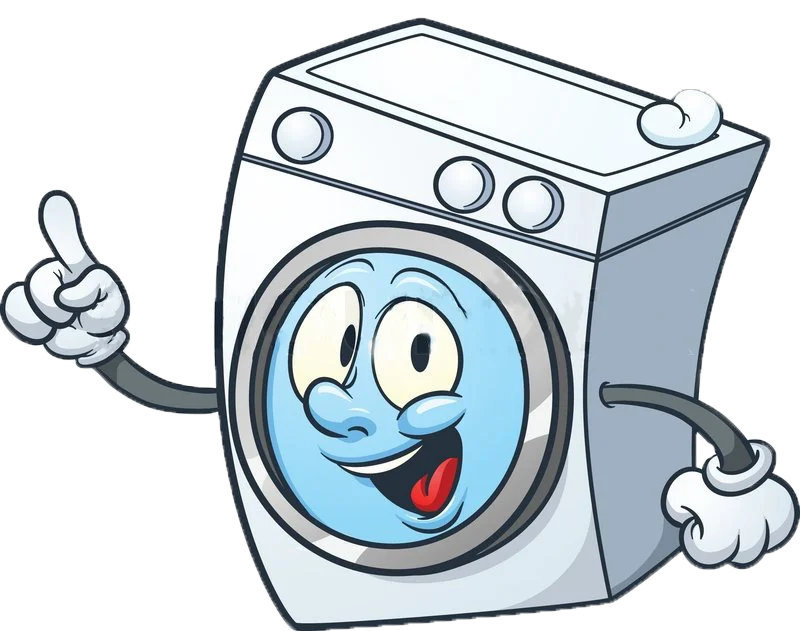
I. Introduction to Washing Machine Commercial Appliance Repair
A. Significance of Well-Functioning Washing Machines B. Overview of Crucial Components in Washing Machines
II. Tools and Equipment for Washing Machine Repair
A. Essential Tools for Effective Washing Machine Repairs B. Safety Precautions and Protocols During Repairs
III. Common Washing Machine Issues
A. Addressing Start-up Problems and Power-Related Concerns B. Dealing with Drainage Issues or Inadequate Water Filling C. Tackling Drum Issues – No Spinning or Agitating D. Investigating Unusual Sounds and Vibrations E. Resolving Water Leakage and Overflows
IV. Fault Finding and Troubleshooting Process
A. Initial Assessment of the Problem
1. Checking Power Supply and Electrical Connections 2. Gathering Comprehensive Problem Descriptions from Users
B. Effective Utilization of Diagnostic Tools 1. Employing Multimeters for Thorough Electrical Checks 2. Analyzing Filters and Components for Potential Blockages
C. Identifying the Root Cause of the Issue 1. Power Problems: Examination of Door Lock, Mainboard, or Timer 2. Water-Related Troubles: Inspection of Drain Pump, Inlet Valve 3. Drum Concerns: Evaluation of Drive Belt, Motor, Drum Bearings 4. Noise and Vibration: Scrutinizing Shock Absorbers, Springs, Motor 5. Water Management Issues: Investigating Hoses, Tub Seal, Pump
D. Systematic Troubleshooting Steps 1. Isolating the Specific Culprit Affecting Performance 2. Thorough Testing and Skillful Replacement of Malfunctioning Components
E. Proper Reassembly and Rigorous Final Testing 1. Skillful Reassembly Techniques and Thorough Cleanup 2. Comprehensive Testing of Washing and Spinning Functionalities
V. Tips for Effective Washing Machine Repairs
A. Prioritizing Safety When Handling Electrical Parts B. Documenting Disassembly Processes and Wiring Connections C. Grasping the Essential Principles of Washing Machine Operation
VI. Advanced Troubleshooting Strategies
A. Addressing Advanced Electronic Control Board and Sensor Issues 1. In-Depth Examination of Electronic Circuits and Wiring B. Diagnosing Water Inlet and Drainage System Challenges 1. Detecting and Resolving Blockages and Leaks
VII. Skill Development and Practical Experience
A. Learning from Real-Life Repair Scenarios and Complexities B. Building Confidence Through Hands-On Engagement C. Staying Abreast of Evolving Washing Machine Technological Trends
VIII. Conclusion
A. Recognizing the Value of Expertise in Washing Machine Repair B. Encouragement to Embrace Ongoing Learning and Exploration
Feel free to enrich each section with your insights, tips, and explanations to create a comprehensive washing machine repair guide.
Electrical Oven Appliances Repair Blog
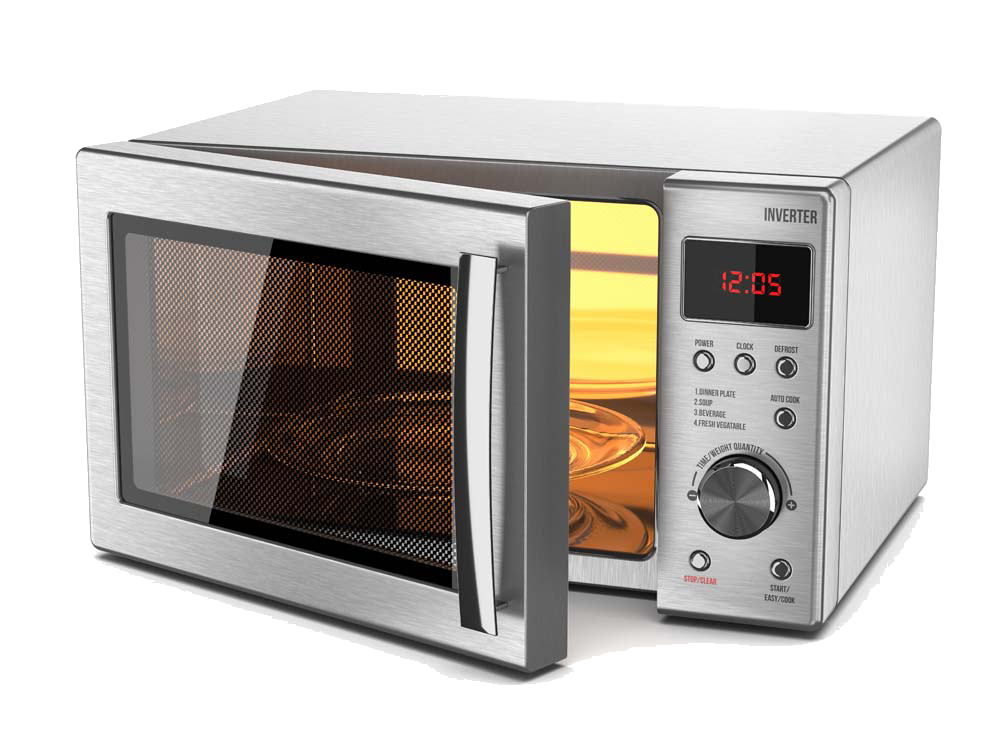
A. Address common issues faced by electrical ovens, such as temperature inconsistencies, malfunctioning controls, or uneven baking. B. Offer troubleshooting techniques specific to electrical ovens, including calibrating temperature settings, checking heating elements, or replacing faulty sensors. C. Emphasize safety precautions, such as disconnecting power before any repairs, and advise readers to consult professionals for complex electrical repairs.
Electrical Oven Repair Guide: Fault Finding and Troubleshooting
I. Introduction to Electrical Oven Repair
A. Significance of Functional Electrical Ovens B. Overview of Crucial Components in Electrical Ovens
II. Tools and Equipment for Electrical Oven Repair
A. Essential Tools for Effective Oven Repairs B. Safety Protocols and Precautions During Repairs
III. Common Issues in Electrical Ovens
A. Addressing Heating Issues and Abnormal Overheating
B. Dealing with Uneven Cooking or Baking Outcomes
C. Troubleshooting Faulty Timers and Control Mechanisms
D. Rectifying Defective Oven Lights or Display Units
E. Investigating Smoke or Unpleasant Odors During Operation
IV. Fault Finding and Troubleshooting Process
A. Initial Issue Assessment
1.check Steady Power Supply and Stable Electrical Connections 2. Acquiring Comprehensive Problem Descriptions from Users
B. Utilizing Diagnostic Tools
1. Employing Multimeters for Comprehensive Electrical Inspections 2. Using Precision Thermometers for Accurate Temperature Readings
C. Identifying the Underlying Fault
1. Addressing Heating Problems: Assessing Heating Elements, Thermostats, Relays 2. Solving Uneven Cooking: Scrutinizing Convection Fans, Airflow, Temperature Sensors 3. Control System Malfunctions: Examining Electronic Control Boards, Knobs, Buttons 4. Display and Light Issues: Investigating Bulbs, Wiring, Display Panels 5. Smoke or Odor Issues: Analyzing Residue, Ensuring Adequate Ventilation
D. Methodical Troubleshooting Approach
1. Isolating the Specific Culprit Impacting Performance 2. Thorough Testing and Skillful Replacement of Faulty Components
E. Skillful Reassembly and Comprehensive Final Testing
1. Proper Reassembly Techniques and Thorough Cleaning 2. Rigorous Testing of Heating and Control Functions
V. Tips for Effective Electrical Oven Repairs
A. Prioritizing Safety When Dealing with High Temperatures
B. Documenting Disassembly Steps and Wiring Connections
C. Understanding the Fundamentals of Oven Heating Elements and Circuits
VI. Advanced Troubleshooting Strategies
A. Addressing Complex Control Board and Sensor Problems 1. In-Depth Examination of Electronic Circuits and Wiring B. Diagnosing Elaborate Temperature Regulation and Fan Dysfunction 1. Identifying and Rectifying Temperature Sensor and Fan Irregularities
VII. Skill Development and Practical Expertise
A. Learning from Real-Life Repair Scenarios and Complexities B. Gaining Confidence Through Hands-On Engagements C. Staying Informed About Advancements in Oven Technology
VIII. Conclusion
A. Recognizing the Value of Expertise in Electrical Oven Repair B. Encouragement to Embrace Continuous Learning and Exploration
Feel free to enrich each section with your insights, tips, and explanations to create a comprehensive electrical oven repair guide.
Dishwasher Appliances Repair Blog
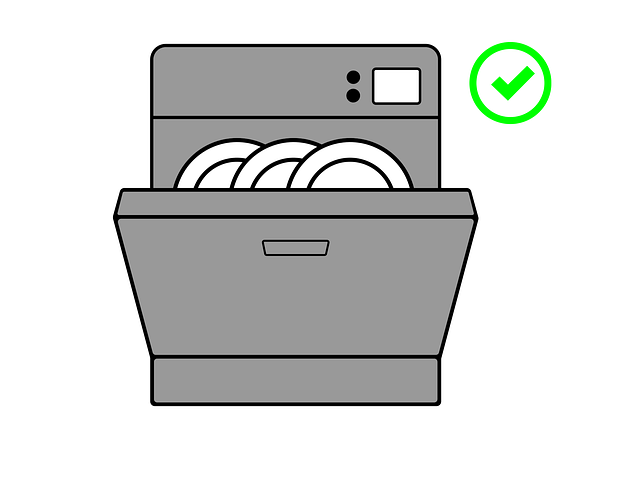
Dishwasher Repair Guide: Fault Finding and Troubleshooting
I. Introduction to Dishwasher Repair
A. Understanding the Significance of Functional Dishwashers B. Overview of Essential Components in Dishwashers
II. Tools and Equipment for Dishwasher Repair
A. Key Tools Required for Effective Dishwasher Repairs B. Safety Measures and Precautions During Repairs
III. Common Issues in Dishwashers
A. Addressing Dishwasher Not Starting or Power-Related Problems B. Dealing with Inadequate Cleaning or Poor Washing Results C. Troubleshooting Faulty Drainage or Water Filling D. Rectifying Control Panel and Display Malfunctions E. Investigating Leaks or Unusual Noises During Operation
IV. Fault Finding and Troubleshooting Process
A. Initial Issue Assessment
1. Verifying Power Supply and Electrical Connections 2. Gathering Detailed Problem Descriptions from Users
B. Effective Utilization of Diagnostic Tools 1. Using Multimeters for Electrical Component Checks 2. Employing Water Pressure Gauges for Plumbing Evaluation
C. Identifying the Fault 1. Power Problems: Assessing Door Lock, Electrical Connections, or Control Boards 2. Cleaning and Washing Issues: Inspecting Spray Arms, Filters, Water Inlet Valve 3. Drainage and Water Filling Troubles: Examining Drain Pump, Float Switch, Valve 4. Control Panel Malfunctions: Investigating Electronic Controls, Buttons 5. Leakage and Noises: Scrutinizing Door Seal, Pump, Hoses, Motor
D. Step-by-Step Troubleshooting Approach 1. Isolating the Specific Culprit Affecting Dishwasher Performance 2. Thorough Testing and Replacement of Malfunctioning Components
E. Reassembly and Final Testing 1. Skillful Reassembly Techniques and Thorough Cleanup 2. Comprehensive Testing of Washing, Draining, and Drying Functions
V. Tips for Effective Dishwasher Repairs
A. Ensuring Safety While Working with Water and Electrical Parts B. Documenting Disassembly Steps and Wiring Connections C. Grasping the Basics of Dishwasher Operation and Water Flow
VI. Advanced Troubleshooting Strategies
A. Addressing Complex Control Board and Sensor Problems 1. In-Depth Examination of Electronic Circuits and Wiring B. Diagnosing Elaborate Water Inlet and Drainage System Issues 1. Identifying and Resolving Blockages, Valve, and Pump Problems
VII. Skill Development and Practical Experience
A. Learning from Real-Life Repair Scenarios and Challenges B. Building Confidence Through Hands-On Practice C. Staying Updated with Dishwasher Technology Advancements
VIII. Conclusion
A. Recognizing the Value of Proficiency in Dishwasher Repair B. Encouragement to Embrace Continuous Learning and Exploration
Feel free to expand on each section with your insights, tips, and explanations to create a comprehensive dishwasher repair guide.
Laser printer Appliance Repair Blog
Laser Printer Repair Guide: Fault Finding and Troubleshooting

I. Introduction to Laser Printer Repair
A. Recognizing the Importance of Operational Laser Printers B. Overview of Vital Components within Laser Printers
II. Tools and Equipment for Laser Printer Repair
A. Essential Tools Essential for Efficient Printer Repairs B. Observing Safety Protocols and Guidelines throughout Repairs
III. Common Laser Printer Issues
A. Addressing Non-Printing or Power-Related Concerns B. Tackling Print Quality Degradation and Fading Prints C. Investigating Paper Jams and Paper Feeding Anomalies D. Troubleshooting Control Panel and Display Irregularities E. Delving into Unusual Noises and Deciphering Error Codes
IV. Fault Finding and Troubleshooting Process
A. Initial Problem Assessment
1. Validating Power Connectivity and Electrical Attachments 2. Extracting Detailed Issue Descriptions from Users
B. Efficient Utilization of Diagnostic Tools
1. Employing Test Pages to Gauge Initial Print Quality 2. Utilizing Multimeters for Rigorous Electrical Component Evaluation
C. Identifying the Underlying Fault
1. Power and Printing Challenges: Inspecting Power Cord, Control Boards, Toner Cartridge 2. Print Quality Issues: Scrutinizing Toner Cartridge, Imaging Drum, Fuser Unit 3. Paper Management Troubles: Analyzing Paper Trays, Rollers, Paper Guides 4. Control Panel Anomalies: Investigating Display, Buttons, User Interface 5. Unconventional Noises and Error Codes: Delving into Fans, Gears, Sensors, Error Messages
D. Step-by-Step Troubleshooting Approach
1. Isolating the Specific Problem Affecting Printer Performance 2. Thorough Testing and Skillful Replacement of Faulty Components
E. Methodical Reassembly and Exhaustive Final Testing
1. Implementing Precise Reassembly Techniques and Thorough Cleaning 2. Conducting Comprehensive Testing of Printing, Paper Handling, and Interface Functions
V. Tips for Successful Laser Printer Repairs
A. Prioritizing Safety in Dealing with Electrical and Laser Components B. Methodical Documentation of Disassembly Steps and Wiring Connections C. Understanding the Core Principles of Laser Printing Technology
VI. Advanced Troubleshooting Strategies
A. Addressing Complex Control Board and Sensor Problems 1. In-Depth Examination of Electronic Circuits and Wiring B. Diagnosing Intricate Print Quality and Paper Handling Challenges 1. Identifying and Resolving Toner Cartridge, Drum, and Roller Anomalies
VII. Skill Development and Practical Experience
A. Drawing Lessons from Real-Life Repair Scenarios and Complexities B. Cultivating Confidence through Hands-On Learning and Engagement C. Staying Abreast of Progressive Trends in Laser Printer Technology
VIII. Conclusion
A. Recognizing the Value of Expertise in Laser Printer Repair B. Encouragement to Pursue Continuous Learning and Exploration
Feel free to amplify each section with your insights, advice, and explanations to create a comprehensive laser printer repair guide.
Conclusion
A. Recap the key points covered in the blog post, highlighting the importance of troubleshooting and timely repairs for various appliances. B. Encourage readers to try the suggested troubleshooting techniques and solutions, but also remind them to seek professional and Service center help when needed. C. Provide a call-to-action, such as inviting readers to subscribe to the blog or share their own appliance repair experiences in the comments section.
Remember to provide clear instructions, tips, and safety precautions throughout the blog post, and consider including relevant images or diagrams
FAQ
Q: What are some common issues with mobile devices that can be resolved through troubleshooting?
A: Common issues with mobile devices that can often be resolved through troubleshooting or you can visit an authorised service center for more help, including battery drain, frozen screens, connectivity problems, and software glitches. Following specific troubleshooting steps can help address these problems.
Q: How can I fix a refrigerator that is not cooling properly?
A: If your refrigerator is not cooling properly, there are several troubleshooting steps you can take. These may include cleaning the condenser coils, checking the temperature settings, ensuring proper door gasket sealing, and defrosting the unit if necessary.
Q: What are some DIY troubleshooting tips for air conditioning units?
A: DIY (Do it yourself)troubleshooting tips for air conditioning units may
involve checking thermostat settings, cleaning or replacing air filters,
inspecting the outdoor unit for debris or obstructions, and ensuring proper airflow. These steps can often help resolve common air conditioning problems.
Q: How can I troubleshoot common washing machine problems?
A: Troubleshooting common washing machine problems may include checking the water supply, inspecting hoses and valves, resetting the machine, and ensuring proper loading techniques. Following these steps can help identify and resolve issues with your washing machine.
Q: What should I do if my electric oven exhibits temperature inconsistencies?
A: If your electrical oven exhibits temperature inconsistencies, there are a few steps you can take. These may include calibrating temperature settings, checking heating elements for damage, or replacing faulty temperature sensors. However, it’s important to exercise caution and consult professionals for complex electrical repairs.
Q: How can I address poor cleaning or water drainage problems in my dishwasher?
A: To address poor cleaning or water drainage problems in a dishwasher, you can try cleaning filters, checking spray arms for blockages, ensuring proper loading techniques, and running cleaning cycles. These steps can help improve the dishwasher’s performance.
Q: Is microwave oven and electric oven the same?
A: A microwave oven uses microwaves and cooks food from the inside, while an electric oven cooks food from the outside. Microwaves cook food much faster than a conventional oven. In a microwave oven, heating is not required longer than 10 minutes. Microwave ovens are expensive and have a high-power usage than electric ovens.